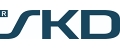
SKD Bojkovice has 2 main production plants (tool shop and plastic press) and focuses on injection moulding manufacturing, pressing and assembly of plastic parts. Our supplies are 100% to the automotive industry.
SKD offers and can provide complete and comprehensive services, service in the field of plastic parts and assembled sub-assemblies. It has a modern and complete machine park.
SKD's work starts from design and development, through prototype moulds and parts, serial moulds, to the production and delivery of plastic parts or assembled sub-assemblies to the customer.
SKD Toolroom is one of the largest tool shops in Europe. It has its own mould making group in China for projects where our customers require it.
Certificates
Quality management systems
Environmental management systems
Quality management system requirements for automotive production and relevant service parts organizations
Assortment / Services
The toolshop producing moulds for technically and visibly demanding parts,including those that have a graining, polished and multi-component parts, overmoulding components with the use of Mucell technology, gas injection etc.
In this section there is the company equipped with a top-quality 3-axis and 5-axis milling centres from company Deckel Maho. It ranges from the smallest Maho Deckel DMU 60 up to the largest one - Maho Deckel DMU 125. As a part of accessories we use also HSC machine Deckel Maho, type DMU75L, 5-axis milling machines from company Fehlmann are used there, namely Picomax 90 with a robot and Picomax 60. These devices are mostly used for production of graphite elecrodes as well as for production of highly precise optical inserts that are parts of moulds.
Company has got four sinkers Charmilles Roboform and three wire-cutting machines from company Mitsubishi. As for the wire-cutting machines, we are able to machine parts having maximum diameters up to 250 x 550 x 600 mm and weight up to3,000 kilogrammes. Sinkers have even bigger range of use for work-pieces and it is up to 850 x 1050 x 550 mm and weight up to 1,600 kilogrammes.
The workplace is equipped with a Reis Robotics TUS 100 press. The moulds are delivered to the customer completely ectified. We perform all forms of testing on our own, as we also own a injection moulding plant, and therefore we are able to offer a complete service to our customers.
Pulse and laser welding are also part of this workshop. Maximum mould size: frame 1 200 x 1 200 mm and maximum weight 8 000 kg.
Injection moulding from 50t up to 900t and a vertical press with a turning table, all presses are equipped with robots. Of which 18x application of 6-axis Kuka robots. To the end of 2018
we have a total of 30 presses. Our own high-speed press Bruderer 25 t for pressing sheet-metal inserts (pressed-in parts) such as contacts, terminals, holes for further overmoulding
process. Undoubtedly, having our own tool shop, Design and construction is a significant advantage.
We process nearly all types od materials, for instance PA66 GF30, PA66 GF50, PPA GF45, PA46 GF40, Grilon PA6 + PA66, PPS, PBT GF30, ABS, ABS/PC,
PC, POM, EPDM, PP, PMMA, PUR and many others.
In addition to injection technology, we also have a lot of other technologies. As ultrasonic and vibrational welding, cryogenic blasting, washing of plastic parts, hot stamping, tampoprinting,
leakage test and a whole range of other assembly and testing facilities.
We use information systems that belong into a category of production-and-information systems; MES system Pharis, which creates an interface between injection moulding
presses and company´s ERP system. Injection moulding workshop has got its own infrastructure and background, namely Quality section, Proces engineering, Warehouses etc.